Der optimale Filter beim thermischen Schneiden
Der optimale Filter beim thermischen Schneiden
Bei thermischen Schneidverfahren macht der Filter die Musik. Laser-, Plasma- und Brennschneideanlagen erzeugen beim Schneiden einen feinen Staub, der eine geeignete Filteranlage erfordert. Hohe Temperaturen des erfassten Staubs und eine sehr feine Körnung von meist weniger als 1 µm sind eine Herausforderung. Herkömmliche Filteranlagen haben Schwierigkeiten, diesen feinen Filterstaub effizient zu handhaben. Normale Schweißrauchfilter mit herkömmlichen Gewebefiltermaterialien sind bereits nach kurzer Zeit verstopft und können nicht mehr gereinigt werden. Beim näheren Hinsehen stellen wir fest, dass es mit Metallpartikeln verklebt ist, die nicht mehr entfernt werden können.
Die in diesem Bereich eingesetzten Entstaubungsanlagen arbeiten nach dem Prinzip der Oberflächenfilterung. Dabei werden Systeme eingesetzt, die feine Stäube effektiv entfernen und somit die Gesundheits- und Umweltbelastung auf ein Minimum senken. Ebenso schützen die Anlagen die Werkhallen und Maschinen, wo sich sonst ein feiner grauer Schleier überall ausbreiten würde. Ist das der Fall, sollte man in erster Reihe die Filter überprüfen, denn wahrscheinlich liegt es genau daran.
Es gibt verschiedene Arten von Filtersystemen, die für diese Aufgabe eingesetzt werden können. Im Folgenden werden wir einen kurzen Überblick über die einzelnen Systeme geben und ihre Vor- und Nachteile erläutern.
- Patronenfilter: Patronenfilter sind die am häufigsten eingesetzten Filtersysteme bei thermischen Schneidanlagen. Sie bieten eine große Filteroberfläche und können Dank der kompakten Bauformen auf kleinen Stellflächen installiert werden. Die Handhabung und der Wechsel der Filterelemente sind in der Regel einfach. Allerdings erfordern sie einen höheren Differenzdruck und eine höhere Leistungsaufnahme der Motoren, da sie mit einer Oberflächenbeschichtung arbeiten, um den Staub aufzufangen.
- Gewebefilter: Gewebefilter können ebenfalls zur Filtration von Stäuben bei thermischen Schneidanlagen eingesetzt werden. Sie bieten eine gute Filterwirkung, wenn ihre Oberfläche und die Strömungsgeschwindigkeiten richtig dimensioniert sind. Gewebefilter sind in der Regel kostengünstiger und erfordern weniger Wartung. Allerdings können sie bei feinem Staub schneller verstopfen und müssen regelmäßig gereinigt oder ausgetauscht werden.
- Nassabscheider: Nasswäscher sind eine Alternative zu den oben genannten Filtersystemen. Sie erfassen den Staub mittels eines Wasserbads und binden ihn dort. Nasswäscher sind wartungsfreundlich und haben niedrige Betriebskosten. Sie bieten jedoch eine geringere Filterwirkung und erfordern eine Ableitung der Abluft nach außen.
Die bewährteste Methode
Entstaubungsanlagen ausgestattet mit Patronenfilter sind in der Regel die am häufigsten verwendeten Filtersysteme für den Einsatz an thermischen Schneidanlagen. Große Filterflächen und ein einfacher Austausch der Filterelemente sind nur eine Seite der Münze. Je nach Anlagenhersteller variieren die Formen und Flanschanschlüsse der Filterpatronen.
Rund, rund mit Haken- oder Gewindebolzen-Flansch, oval, konisch zulaufend oder wie in unserem nachfolgenden Fall in einer Nederman-Anlage flach. Auch unter dem Begriff „Fillteplatte” zu finden. Die optische Ausführung hat jedoch keinen nennenswerten Einfluss auf die Leistungsfähigkeit.
Es gibt zwei Arten von Patronenfilterkonzepten für die Filterung von Stäuben beim thermischen Schneideprozess: Filterpatronen mit Oberflächenbeschichtung, den sogenannten perkutierten Filter und Filterpatronen ohne Oberflächenbeschichtung. Bei der Oberflächenbeschichtung wird das Filtermaterial außenwandig beschichtet, um den feinen Staub auf der Oberfläche zu binden. Je nach eingesetztem Precoat und Filterart werden auf die Oberfläche zwischen 5g- 250g pro Quadratmeter Filterfläche des Pulvers aufgetragen. Die Funktionsweise sehen wir in der nachfolgenden Grafik.

Die Filtersysteme ohne Oberflächenbeschichtung sind in der Regel kostengünstiger und erfordern weniger Wartung. Sie arbeiten jedoch mit anderen Differenzdrücken und Strömungsgeschwindigkeiten.
Die Oberflächenbeschichtung dient dazu, den Feinstaub auf der Oberfläche des Filters zu halten und ermöglicht eine automatische Reinigung mittels Druckluftstoß. Oberflächenbeschichtete Filter erfordern aufgrund der geringen Luftdurchlässigkeit des Materials höhere Differenzdrücke und daher eine höhere Leistungsaufnahme der Motoren. Hier ein Beispiel. Ein 180g/m² Polyestergewebe ohne Beschichtung hat eine Luftdurchlässigkeit von 720 m³/m²/h. Ein Polyestergewebe mit PTFE- Beschichtung lässt noch 410 m³/m²/h und beim Material Polyester PTFE-Membrane liegt der Wert nur noch bei 288 m³/m²/h. Optisch und haptisch sind die Materialien für Laien kaum zu unterscheiden. Siehe Bild.

Wie erkenne ich, dass die Filterpatrone einwandfrei funktioniert?
Ein Beispiel aus der Praxis bei unserem Kunden. Verbaut wurden Polyester PTFE-Beschichtete Luftfilter mit einem thermischen Widerstand von 120°C in einer Nederman-Absauganlage.
Ob ein Filter einwandfrei funktioniert, können wir auch schon mit dem bloßen Auge erkennen, wie nachfolgenden auf Bildern auch zu sehen ist.
- In erster Linie sollte die Partikelverteilung gleichmäßig über die komplette Filterfläche stattfinden.
- Zweitens sollten sich die Partikel durch Berührung ohne größeren Aufwand vom Filter lösen lassen. Sollte das nicht der Fall sein, sind eventuell Partikel mit dem Material verschmolzen. Der Filter wird dadurch unbrauchbar.
- Ebenfalls sollte die Filterpatrone im inneren sauber sein. Das bedeutet, dass keine Schmutzpartikel durch das Material gedrungen sind und auch keine Risse oder andere mechanische Beschädigungen vorhanden sind.

Mögliche Störungen durch geringere Luftdurchlässigkeit einer Patrone
Es kommt manchmal vor, dass die Absauganlagen bei neuen Patronen eine Störmeldung auslösen. In der Regel handelt es sich um die Meldung „Filter verstopft". Die Ursache liegt jedoch nicht am Filter. In diesem Fall müssen die Einstellungen der Anlage angepasst werden. Es kommt auch vor, dass die Druckdosen oder Ventilmembranen fehlerhaft sind und ausgetauscht werden müssen. Danach funktionieren die Anlagen wieder einwandfrei.
Ein weiteres Problem, das Auftreten kann, hat mit der Abreinigung zu tun. Durch den geringeren Luftdurchsatz den die Filter ermöglichen, müssen die Anlagen mehr Leistung aufwänden, um eine effektive Reinigung zu gewährleisten. Im ersten Schritt sollte geprüft werden, ob die Partikel durch Berührung einfach abfallen. Ist das gegeben, müssen die Einstellungen der Anlage angepasst werden. Es kommt auch vor, dass die Ventilmembranen fehlerhaft sind und ausgetauscht werden müssen. Danach funktionieren die Anlagen wieder einwandfrei.
Ein weiterer Faktor, der mit einem hochwertigeren Material einhergeht, ist die Abnahme der Filterfläche auf einer Filterpatrone. Das „dickere" Material nimmt beim Plissieren (Falten des Filtermaterials) mehr Platz ein und so sinkt die Materialmenge, die auf eine Patrone verarbeitet werden kann.
Fazit
Die Auswahl des richtigen Filtersystems hängt von verschiedenen Faktoren ab, wie z.B. den spezifischen Anforderungen der Schneidanlage, der Umgebung und dem Budget. Es ist wichtig die Filterleistung, die Wartungsintervalle, die Energieeffizienz und die Betriebskosten bei der Entscheidung zu berücksichtigen. Ein gut dimensioniertes und regelmäßig gewartetes Filtersystem ist unerlässlich für einen effizienten und umweltverträglichen Betrieb einer thermischen Schneidanlage.
Denken Sie daran, dass ein gut funktionierendes Filtersystem den Schutz der Umwelt, die Sicherheit der Mitarbeiter und die Einhaltung von Vorschriften gewährleistet.
Bei der Auswahl der passenden Filter sollte auf die spezifischen Anforderungen geachtet werden. Die richtige Dimensionierung und Wartung des Filtersystems ist entscheidend für einen zuverlässigen und umweltverträglichen Betrieb einer thermischen Schneidanlage.
Lange Erfahrung, eine große Auswahl an Filtermaterialien, Filterausführungen und der enge Kundenkontakt machen uns zu einem starken Partner. Wir helfen und beraten Sie gerne bei der Auswahl des passenden Filters. Schreiben Sie uns oder rufen direkt an.
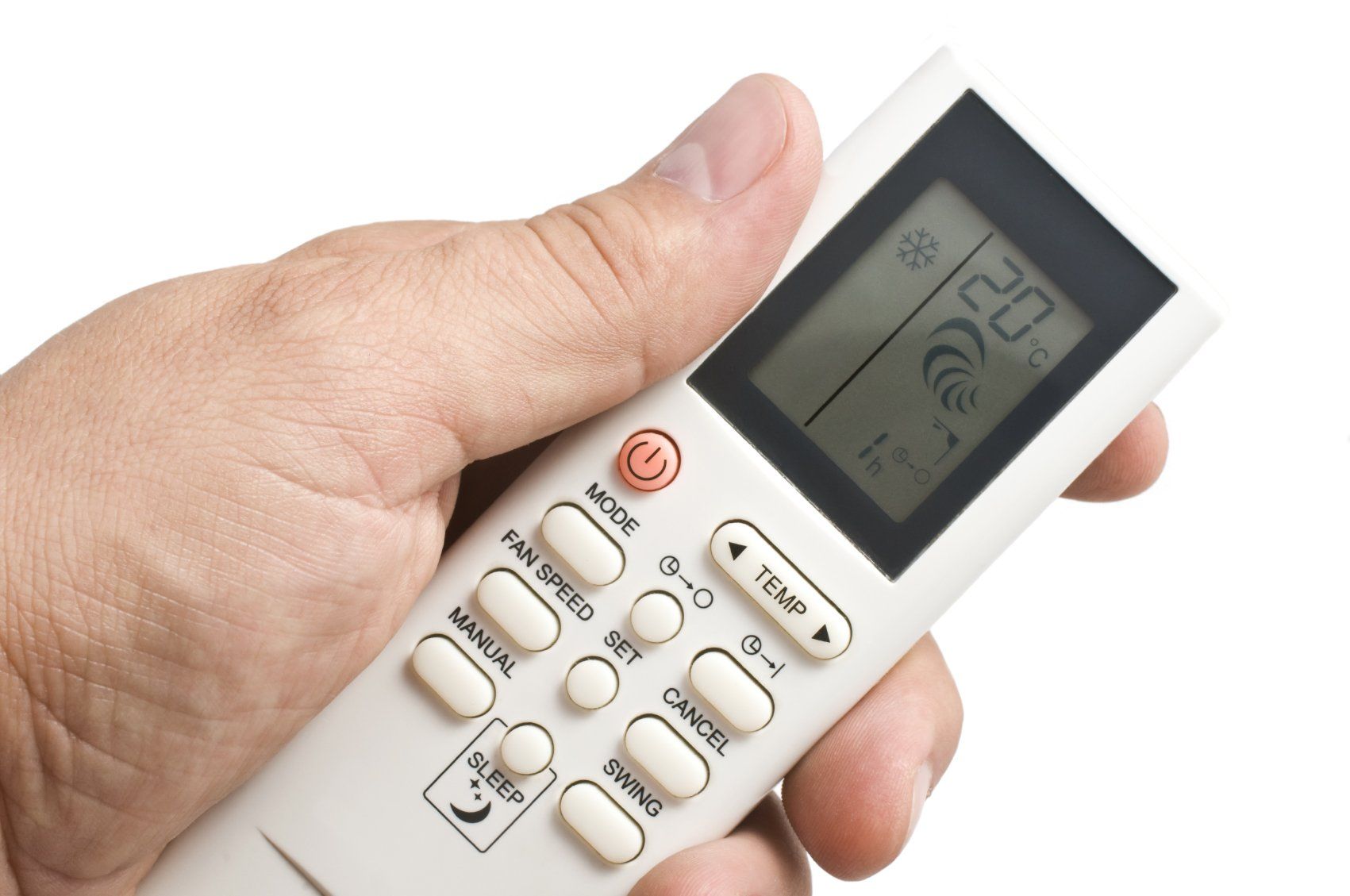


